초경합금은 높은 경도, 우수한 내마모성, 내 부식성 및 작은 열팽창 계수의 가장자리를 가지고 있습니다. 광학 유리 성형, 금속 드로잉 및 내마모성 및 내식성 부품과 같은 정밀 금형의 제조에 널리 사용됩니다. 초경합금 금형은 수명이 길고 철강 금형보다 10 배 이상 또는 수백 배 이상 높을뿐만 아니라 표면 품질이 매우 우수합니다. 유리 렌즈 및 기타 사출 성형 부품은 광학 표면 품질 요구 사항을 충족 할 수 있습니다.
초경합금은 가공성이 열악하여 일반적으로 재료를 가공하기가 어렵습니다. 연삭 및 EDM은 초경 다이의 가장 일반적으로 사용되는 가공 방법 중 하나입니다. CBN, 다이아몬드 및 기타 초경량 공구의 출현으로 초경합금을 직접 절단 할 수있어 점점 더 많은 관심을 끌고 있습니다. 외국 학자들이 더 많은 연구를 수행했습니다. B. bulla et al. 다이아몬드 터닝에서 초경합금의 표면 프로파일에 대한 가공 매개 변수의 영향을 분석했습니다. 최적의 가공 매개 변수를 얻은 후 표면 거칠기와 공구 마모에 대한 공구 형상의 영향을 자세히 조사했습니다. 스즈키 등 초경합금에 대한 다이아몬드 초음파 타원형 진동 터닝 실험을 수행했습니다. 초음파 타원 진동 선삭의 표면 품질이 일반 선삭의 표면 품질보다 우수하고 공구 마모가 더 작습니다. 실험을 통해 마이크로 프리즘 및 광학 표면 품질의 구면 렌즈와 같은 경질 합금 다이도 가공되었습니다.
정확하고 복잡하며 수명이 긴 초경합금 다이를 제조하기 위해서는 국가 다이의 제조 수준을 측정하는 것이 중요하다. 마이크로 밀링 기술은 높은 가공 효율, 광범위한 가공 재료, 3 차원 복합 형상 가공, 높은 표면 품질 등의 장점을 가지고 있습니다. 초경합금 초소형 및 초소형 부품 가공에 매우 적합하며 광범위한 응용 가능성을 가지고 있습니다. 이 논문에서 다이아몬드 코팅 공구는 초경합금의 미세 밀링에 사용됩니다. 절삭력, 표면 품질 및 공구 마모가 분석됩니다.
PDC 마이크로 밀링 테스트 장비 및 실험 일정
자체 제작 된 고정밀 마이크로 밀링 머신 툴 (그림 1 참조)이 사용됩니다. 공작 기계는 소형 및 미세 부품의 미세 밀링을 위해 특별히 설계되었습니다. 대리석 베드, 급지 장치, 고속 공기 부양 스핀들, PMAC 기반의 모션 제어 시스템 등으로 구성되어 있습니다. 마이크로 밀링 커터의 작은 직경으로 인해 정확한 공구 설정이 쉽지 않습니다. 공작 기계에는 온라인으로 마이크로 밀링 공정을 모니터링하는 데 사용할 수있는 현미경 도구 설정 시스템이 장착되어 있습니다.

그림 1 마이크로 밀링 머신
나선형 모서리가있는 다이아몬드 코팅 마이크로 밀링 커터를 사용하십시오 (그림 2a 참조). 절단기의 기재는 경질 합금이고, 다이아몬드 막 층은 화학 기상 증착 (CVD)에 의해 코팅된다. 핸들 직경은 6mm, 블레이드 직경은 1mm, 블레이드 길이는 2mm, 공구의 전면 각도는 2 °, 후면 각도는 14 °, 나선형 각도는 35 °입니다. SEM 측면에서 측정 한 툴팁 호 반경 γε은 약 11μm입니다 (그림 2b 참조). SEM 평면도로부터 측정 된 공구 날 아크 반경 γβ는 약 8 μm이다 (도 2C 참조).

(a) (b)
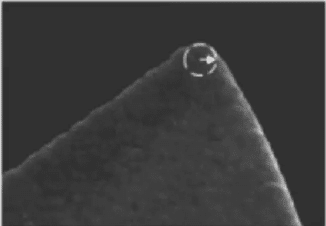
(씨)
그림 2 다이아몬드 코팅 마이크로 밀링 커터
다이아몬드 코팅 공구는 다양한 가공 매개 변수에서 직선 홈을 밀링하는 데 사용됩니다. 테스트 전에 공작물의 표면을 연마 한 다음 측정 기기에 고정 및 고정하고 샘플링 주파수는 20kHz입니다. 모든 테스트는 건식 절단 조건에서 수행됩니다. 마이크로 밀링 테스트 매개 변수에 대해서는 표 1을 참조하십시오. 스핀들 속도 n은 20000r / min으로 고정되고 밀링 깊이 AP는 2μm와 4μm이며 각 톱니 FZ의 이송 속도는 0.3-1.5μM입니다. 테스트 후 초음파 세척기를 사용하여 세척 공작물. Mahr 표면 거칠기 측정기를 사용하여 이송 방향을 따라 가공 된 표면 거칠기 및 마이크로 프로파일 곡선을 측정했습니다. 가공 된 표면 형태 및 공구 마모 형태는 SEM에 의해 관찰되었다.
테스트 결과 및 분석 PCD 마이크로 밀링
밀링 포스 신호는 밀링 프로세스를 모니터링하는 데 중요한 매개 변수로, 공구 마모 상태와 가공 표면 품질을 실시간으로 반영 할 수 있습니다. 밀링 공정에서 절삭 두께는 연속적으로 변경되어 밀링 커터의 회전에 따라 0에서 최대로 증가한 다음 주기적으로 0으로 감소하여 밀링 힘 신호의 웨이브 트로프 및 웨이브 피크가 발생합니다. 밀링 힘 신호의 파형에서 가공 과정에서 고르지 않은 절단 및 진동과 같은 비정상적인 동작을 관찰 할 수 있습니다.
그림 3은 테스트에 의해 측정 된 밀링 힘 신호의 파형도이며, 여기서 Fx는 주 절삭력이고 Fy는 이송 력이며 Fz는 축력입니다. 밀링 력의 파형에서 볼 수 있듯이 축력의 진폭 Fz는 밀링 프로세스의 세 가지 구성 요소에서 다른 두 가지 구성 요소보다 훨씬 더 크며, 주 절삭력 Fx와 최소 이송 력 Fy가 가장 크다는 것을 알 수 있습니다. 그 이유는 마이크로 밀링에서 밀링 깊이 AP가 매우 작아서 마이크로 밀링 커터의 팁 아크 γ ε의 반경보다 훨씬 작기 때문입니다. 팁 아크 하단의 작은 부분 만 실제로 절단에 관여하며, 이는 작은 주 편향 각을 갖는 절단과 동등하며, 축 방향 밀링 힘 성분이 커집니다.
밀링 커터가 회전 할 때마다 두 개의 대칭 절삭 날이 절삭에 연속적으로 참여하여 밀링 힘 신호주기에서 두 개의 파동 피크를 나타냅니다. 오실로 그램에서 두 피크의 진폭이 동일하지 않으며 상반기의 진폭이 후반보다 분명히 크다는 것을 알 수 있습니다. 이는 실제 밀링 공정에서 이중 치 밀링 커터의 두 절삭 날의 절삭 두께가 다르고 한 절삭 날에 더 많은 재료가 있고 다른 절삭 날에 재료가 적어 밀링 현상이 고르지 않음을 보여줍니다. 심각한 불균일 밀링은 밀링 힘의 변동을 유발하고 가공 과정에서 진동을 증가시켜 미세 밀링의 안정성에 영향을 미치지 않습니다.

그림 3 마이크로 밀링 힘 신호 파형
﹣ 테스트 중에 다양한 미세 밀링 매개변수에서 밀링 힘이 기록됩니다. 공구 회전 사이클에서 최대 절삭 두께에 해당하는 밀링력의 피크 값을 테스트 결과로 취하고 X, y 및 Z 성분의 측정 결과를 그림 4에 나타내었다. 동일한 밀링 깊이에서 밀링력 각 톱니의 이송 속도 FZ가 증가함에 따라 증가합니다. 주절삭력(Fx)과 이송력(Fy)은 비교적 완만하게 상승한다. 밀링 깊이가 ap=2m 및 4m일 때 주절삭력 Fx는 각각 0.44N 및 0.92N에서 1.34N 및 2.05N으로 증가하고 이송력 Fy는 1.34N 및 두 번째에서 "Ho " 그리고"; 축 방향 힘은 "Qi"와 "the"에서 "the"로 큰 진폭으로 증가합니다. 유사하게, 밀링 깊이의 증가는 밀링 힘의 증가로 이어질 것입니다. 3방향 구성요소의 축방향 힘 FZ는 밀링 매개변수에 민감합니다. 그 이유는 마이크로 밀링에서 각 톱니 FZ의 이송 속도가 마이크로 밀링 커터의 모서리 호 반경 γ β보다 작아서 마이크로 밀링 커터의 하단 모서리 후면과 공작물 사이의 접촉 영역이 만들어지기 때문입니다. 상대적으로 크고 후면의 마찰력이 밀링력에서 큰 부분을 차지합니다.

가공 파라미터에 따른 밀링 힘의 그림 4 곡선
표면 품질 PCD 마이크로 밀링
초경합금은 일종의 단단한 취성 재료입니다. 전통적인 절단에서, 단단한 취성 재료는 일반적으로 취성 파괴의 형태로 제거되어 기계 가공 표면에 취성 파괴 결함을 초래하고 기계 가공 표면의 품질에 영향을 미친다. 결과는 절삭 두께가 특정 임계 값보다 작도록 가공 파라미터가 제어 될 때 취성 재료가 소성 변형을 가질 수 있고, 연성 절삭이라고하는 매끄러운 연성 가공 표면이 얻어진다는 것을 보여준다. 그림 5는 AP = 2 μm 및 FZ = 1.2 μ M에서 미세 밀링 초경의 표면 형태와 프로파일 곡선을 보여줍니다. 가공 표면 형태는 주로 공구를 사용한 공구 형상의 반영이라는 것을 알 수 있습니다. 마크 텍스처 분포. 형상 곡선에서 공구 톱니의 이송 공구 마크를 확인할 수 있으며 취성 파괴 결함이 거의 없습니다. 미세 밀링에서는 실제 절삭 두께가 매우 작아 초경합금의 연성 절삭을 실현할 수 있습니다. 초경합금 소재는 소성 변형 방식으로 제거되어 우수한 가공 표면 품질을 얻습니다.
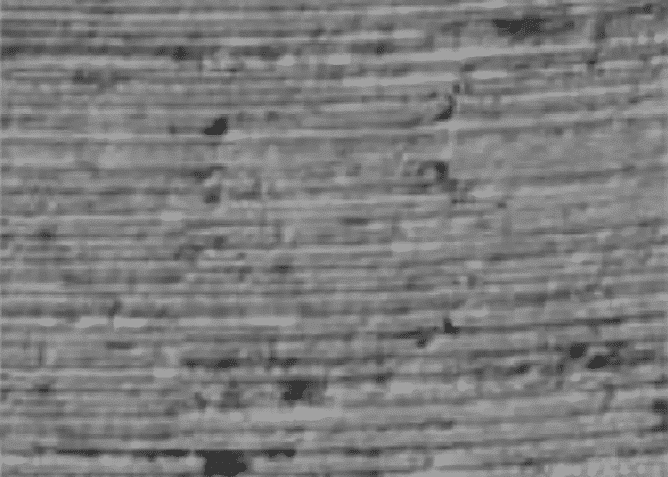
(a) 표면의 형상

(b) 등고선
그림 5 가공 된 표면 형태 및 프로파일
그림 6은 가공 매개 변수가있는 초소형 초경합금의 표면 거칠기 Ra 곡선을 보여줍니다. 그림에서 알 수 있듯이 초경합금의 연성 절삭으로 인해 초경합금 가공 된 표면 거칠기의 Ra 값이 매우 작다는 것을 알 수 있습니다. 톱니 당 피드 AP와 밀링 깊이 FZ가 증가하면 표면 조도 Ra가 증가하지만 표면 조도에 대한 톱니 당 피드의 효과는 밀링 깊이보다 큽니다. AP = 2 μm 및 FZ = 0.3 μm 일 때, 최소 표면 거칠기는 0.073 μm이고; AP = 4 μm 및 FZ = 1.5 μm 인 경우 최대 표면 거칠기는 0.151 μM입니다.

(b) 윤곽
그림 6 가공 표면의 모양과 윤곽
그림 6은 가공 매개 변수가있는 초소형 초경합금의 표면 거칠기 Ra의 변화 곡선을 보여줍니다. 그림에서 알 수 있듯이 초경합금의 연성 절삭으로 인해 초경합금 가공 된 표면 거칠기의 Ra 값이 매우 작다는 것을 알 수 있습니다. 톱니 당 피드 AP와 밀링 깊이 FZ가 증가하면 표면 조도 Ra가 증가하지만 표면 조도에 대한 톱니 당 피드의 효과는 밀링 깊이보다 큽니다. AP = 2 μm 및 FZ = 0.3 μm 일 때, 최소 표면 거칠기는 0.073 μm이고; AP = 4 μm 및 FZ = 1.5 μm 인 경우 최대 표면 거칠기는 0.151 μM입니다.

(a) (b)

(씨)
7 절삭 공구 마모의 미세 형상

표면 거칠기에 대한 밀링 길이의 영향
그림 8은 미세 밀링 경로에 따른 표면 거칠기 곡선을 보여줍니다. 도면에서 볼 수 있듯이 밀링 경로가 증가함에 따라 표면 거칠기 (Ra)가 점차 증가 함을 알 수있다. 밀링 거리가 700m m에 도달하면 표면 거칠기가 크게 증가합니다. 밀링 거리가 700mm를 초과하면 표면 거칠기의 증가가 느려집니다. 밀링 길이가 1000mm 인 경우 표면 거칠기 Ra가 0.224μM에 도달합니다. 공구 마모 후 밀링 력이 증가 할뿐만 아니라 공작물의 압출 및 마찰이 더욱 심해져 시멘트의 취성 파괴 가능성이 높아집니다. 초경 재료는 가공 된 표면에 취성 파괴 결함을 유발하고 가공 된 표면 품질을 악화 시키며 표면 거칠기를 증가시킵니다.
결론
(1) 밀링 깊이가 팁 원호의 반경보다 훨씬 작기 때문에 팁 원호의 맨 아래 만 실제로 절삭에 관여하여 큰 축 방향 부품이 생성됩니다. 다이아몬드로 코팅 된 이중 치형 밀링 커터의 미세 밀링 공정에서 균일하지 않은 밀링 현상이 발생하며 치아 당 이송이 증가하고 밀링 깊이에 따라 밀링 력이 증가합니다.
(2) 미세 밀링이 매우 작아서 초경합금의 연성 절삭을 실현하고 우수한 가공 표면 품질을 얻을 수 있습니다. 톱니 당 이송이 증가하고 밀링 깊이가 증가하면 표면 조도 Ra가 증가합니다.
(3) 2 개의 날이 고르지 않게 마모되고 베어링 날이 심각하게 마모됩니다. 밀링 경로가 증가하면 표면 거칠기가 증가합니다.